Non ci sono prodotti a carrello.
Kevin Keller Product Line Manager (onsemi)
Nonostante il persistere dell’”ansia da rifornimento”, la diffusione dei veicoli elettrici (EV) nelle sue varie forme (ibridi, esculsivamente elettrici, ecc.) sta procedendo a ritmo sostenuto. I produttori automobilistici sono attivamente impegnati ad aumentare l’autonomia dei veicoli e a ridurre i tempi di ricarica per superare questo significativo ostacolo e incrementare ulteriormente il tasso di adozione di tali veicoli. La modalità di ricarica dei veicoli elettrici ha un notevole impatto sulla praticità e fruibilità del veicolo. A causa del numero ancora limitato di stazioni di ricarica ad alta potenza, una larga percentuale di possessori di veicoli elettrici ricorre ancora ai caricatori di bordo (OBC – On Board Charger) per effettuare la ricarica. Per migliorare le prestazioni degli OBC, le Case automobilistiche si stanno orientando verso nuove tecnologie come il carburo di silicio (SiC). Scopo di questo articolo è mettere in luce l’importanza degli OBC e analizzare come l’evoluzione dei commutatori a semiconduttore contribuirà a incrementare in modo significativo le loro prestazioni.
Sul mercato sono disponibili veicoli che utilizzano un’ampia gamma di sistemi di propulsione: da quelli alimentati esclusivamente da un motore a combustione interna (ICE – Internal Combustion Engine) ai modelli ibridi che utilizzano un ICE abbinato a un’alimentazione elettrica (xHEV) ai veicoli elettrici (xEV). I veicoli xHEV, a loro volta, si dividono in due categorie: MHEV (Mild Hybrid EV) e FHEV (Full Hybrid EV).
I veicoli MHEV prevedono la presenza di un motore a combustione interna supportato da una piccola batteria (solitamente a 48 V). Essi non possono viaggiare spinti solamente dal motore elettrico, il quale contribuisce a ridurre (anche se in misura modesta), il consumo di carburante.
I veicoli FHEV, invece, assicurano una maggiore flessibilità in quanto abbinano un motore ICE a un motore elettrico alimentato mediante una batteria (solitamente operante con tensioni comprese tra 100 e 300 V). Anche questo tipo di veicoli effettua la ricarica delle batterie attraverso la frenata rigenerativa, catturando l’energia in fase di frenata per migliorare l’efficienza.
Tutti gli xEVs, inclusi i veicoli ibridi plug-in e quelli alimentati esclusivamente tramite batteria (BEV – Battery EV) sono equipaggiati con sistemi di frenatura rigenerativa. In ogni caso, in considerazione dell’elevata capacità delle batterie, questi veicoli utilizzano in larga misura i caricatori OBC per rifornire le loro batterie.
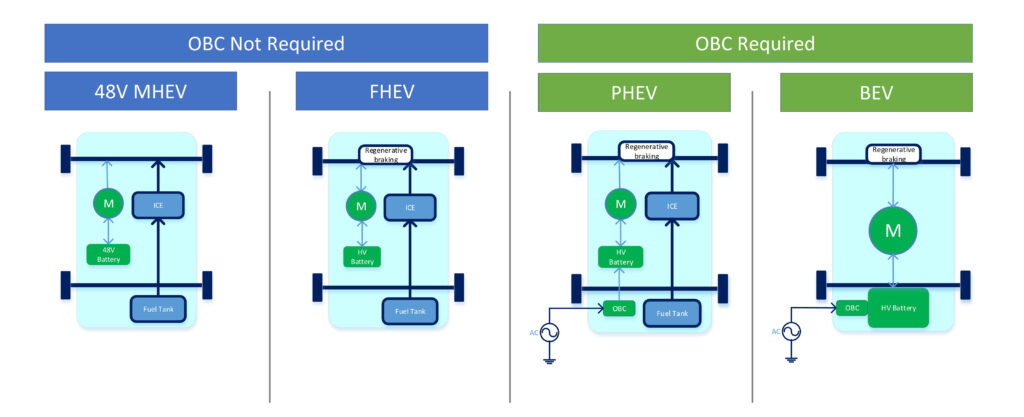
Fig. 1 – Oggigiorno sono disponibili varie tipologie di veicoli elettrici compresi MHEV, FHEV, PHEV e BEV
Il caricabatterie più semplice si presenta sotto forma di un cavo che collega il caricatore di bordo del veicolo elettrico a una presa di corrente (di solito è richiesta una protezione contro i guasti a terra). Anche se conveniente, questa metodologia di ricarica per lo più residenziale (definita nello standard J1772 come SAE AC Level 1) opera con una potenza di circa 1,2 kW e permette di aggiungere un’autonomia pari a circa 5 miglia (poco più di 8 chiliometri) per ogni ora di ricarica. I sistemi di livello 2 (SAE AC Level 2) utilizzano solitamente l’alimentazione AC multi-fase della rete solitamente disponibili negli edifici pubblici e nelle strutture commerciali. Caratterizzata da livelli di potenza fino a 22 kW, questo tipo di ricarica permette di aggiungere un’autonomia massima di 90 miglia (circa 145 km) per ogni ora di ricarica.
Poichè i caricatori di livelli 1 e 2 forniscono corrente alternata (AC) ai veicoili elettrici, il caricatore OBC è indispensabile per convertire l’ingresso in alternata nell’uscita in continua (DC) necessaria per caricare la batteria. La maggior parte dei caricabatteria attualmente in uso è di livello 2.
I caricatori in DC ad alta potenza, noti come caricatori di livello 3, caricatori SAE di livello 1 e 2 o caricatori IEC in modalità 4, forniscono in uscita una tensione continua e permettono quindi di ricaricare direttamente la batteria, eliminando la necessità di un OBC. I livelli di potenza di questi caricatori in DC variano da 50 a 350 kW, in modo da consentire una ricarica fino all’80% della capacità della batteria in 15-20 minuti. In considerazione degli elevati livelli di potenza e delle modifiche infrastrutturali necessarie per la rete elettrica, il numero delle stazioni di ricarica veloce e finora abbastanza limitato, anche se in rapido aumento.
Numerose Case automobilistiche stanno passando dalle batterie a 400 V a quelle a 800 V. Questa transizione è finalizzata all’aumento dell’autonomia dei veicoli elettrici attraverso il miglioramento dell’efficienza del sistema compessivo, l’incremento delle prestazioni, l’aumento della velocità di ricarica e la riduzione del peso sia dei cavi sia delle batterie.
Anatomia di un caricatore OBC
Tipicamente, un caricatore OBC è un convertitore di potenza a due stadi, con uno stadio PFC (Power Factor Correction) seguito da uno stadio di conversione DC-DC isolato. A questo punto val la pena sottolineare che è possibile anche una configurazione non isolata, anche se raramente utilizzata. Lo stadio PFC rettifica l’alimentazione AC, gestisce il fattore di potenza in modo da ottenere un valore superiore a 0,9 e genera una tensione di bus regolata per lo stadio DC-DC.
Negli ultimi anni la richiesta di sistemi bi-direzionali è aumentata in maniera significativa. Sistemi di questo tipo consentono ai veicoli elettrici di invertire il flusso di potenza dalla batteria alla fonte, in modo da supportare varie funzionalità come a esempio il bilanciamento dinamico del carico della rete (V2G – Vehicle-to-Grid) oppure la gestione di eventuali interruzioni di corrente (V2L – Vehicle-to-Load).
L’approccio PFC tradizionale prevede l’utilizzo di un ponte rettificatore a diodi in abbinamento a un convertitore boost. Il ponte retticatore converte la tensione AC in una tensione DC, mentre il convertitore boost ha il compito di aumentare il livello della tensione. Una versione migliorata di questo circuito base è la la topologia boost “interleaved” (interlacciata), che prevede la connessione in parallelo di molteplici stadi di conversione per ridurre la corrente di ondulazione (ripple) e incrementare l’efficienza. Queste topologie PFC utilizzano dispositivi in silicio come a esempio MOSFET a supergiunzione e diodi caratterizzati da bassi valori di tensione diretta (Vf).
L’avvento di commutatori di potenza ad ampia banda proibita (WBG – Wide Band Gap), in modo particolare di quelli realizzati in carburo di silicio (SiC), ha consentito lo sviluppo di nuovi approcci alla progettazione grazie ai vantaggi intrinseci di tali dispositivi, tra cui minori perdite di commutazione, valori ridotti di RDS(on) ed eccellenti caratteristiche di recupero inverso del diodo intrinseco (body Diode).
La topologia totem pole senza ponte (bridgeless) si è affermata nelle applicazioni PFC di media e alta potenza, a partire a 6,6 kW. Lo schema di questa topologia è riportato in figura 2: il ramo più lento (Q5-Q6) commuta alla frequenza della rete (50-60 Hz), mentre quello più veloce (Q1-Q4), che provvede alla formazione (shaping) del segnale e all’aumento della tensione, opera a una frequenza più elevata (in genere compresa tra 65 e 110 kHz) in modalità “hard switching”. A fronte di un significativo incremento dell’efficienza e a una riduzione del numero di componenti di potenza richiesto, la topologia totem pole di tipo bridgeless risulta più complessa in termini di controllo.
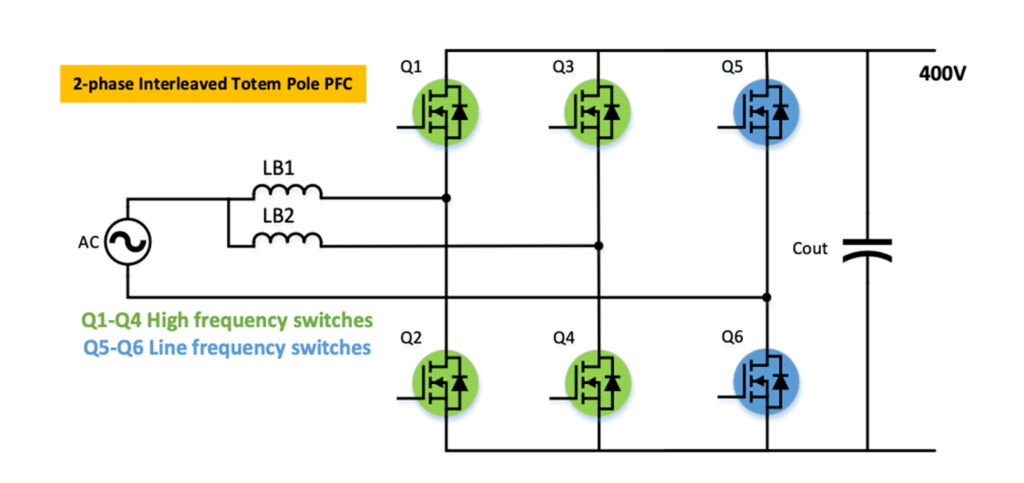
Fig. 2 – Schema della topologia totem-pole “bridgeless”
Per lo stadio DC-DC si adotta solitamente una topologia isolata, utilizzando un trasformatore per l’isolamento, con l’obiettivo prioritario di regolare la tensione di uscita in base allo stato di carica della batteria. Nonostante sia possibile utilizzare topologie a semiponte (half-bridge), la maggior parte delle soluzioni attuali è basata su convertitori DAB (Dual Active Bridge), come i convertitori risonanti (del tipo LLC e CLLC) o i convetitori PSFB (Phase-Shifted Full Bridge). I convertitori risonanti, LCC e CLLC in particolare, hanno attirato l’attenzione grazie ai loro numerosi vantaggi, tra cui l’ampia gamma di funzionamento in modalità “soft switching”, la possibilità di operare in modo bidirezionale e la semplicità di integrazione del trasformatore e dell’induttore risonante in un unico trasformatore di potenza.
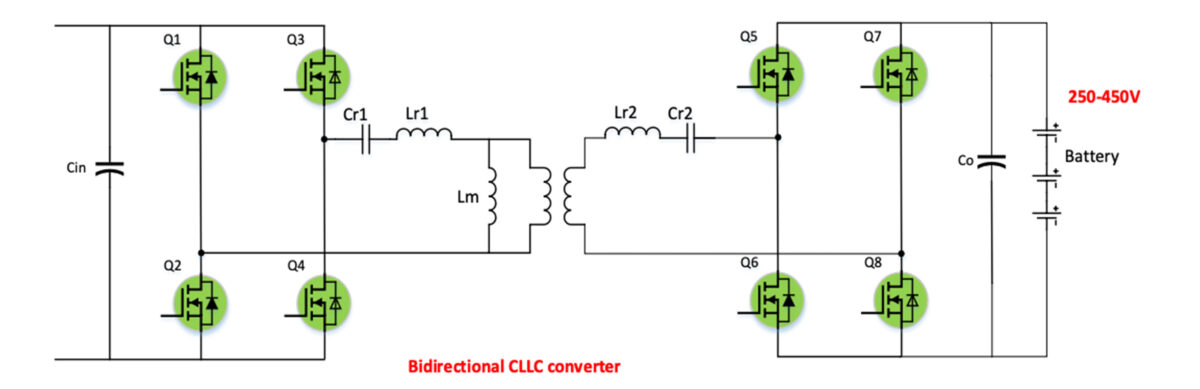
Fig. 3 – Un convertitore DC-DC bidirezionale consente di restituire energia alla rete durante i picchi della domanda
Il carburo di silicio nelle applicazioni OBC
I dispositivi SiC da 650 V sono tipicamente la scelta preferita per i pacchi batteria da 400 V. Tuttavia, nel caso delle architetture che prevedono batterie da 800 V, a causa della maggior tensione richiesta è necessario il ricorso a dispositivi con tensione nominale di 1200 V.
L’utilizzo del carburo di silicio per i caricatori di bordo è ascrivibile alle sue eccellenti prestazioni relativamente a parecchie figure di merito (FoM – Figures of Merit). L’adozione del SiC comporta numerosi vantaggi in termini di RDS(on) specifica per area, perdite di commutazione, caratteristiche di recupero inverso del diodo e tensione di rottura (breakdown). Ciò consente alle soluzioni basate su SiC di operare in maniera affidabile a temperature più elevate. Le migliori prestazioni ottenibili permettono di sviluppare progetti caratterizzati da una maggiore efficienza e un peso inferiore. Di conseguenza, è possibile realizzare sistemi in grado di raggiungere livelli di potenza più elevati (fino a 22 kW) che non potrebbero essere implementati mediante le soluzioni tradizionali basate su silicio (IGBT o MOSFET a super-giunzione).
Anche se un caricatore di bordo di potenza più elevata potrebbe non avere un impatto diretto sull’autonomia di un veicolo elettrico, il suo ruolo è fondamentale per affrontare in maniera efficace il problema dell’ansia da rifornimento, riducendo sensibilmente i tempi di ricarica. Il livello di potenza degli OBC è in continuo aumento, al fine di assicurare tempi di ricarica sempre più rapidi. La tecnologia SiC svolge un ruolo fondamentale per migliorare l’efficienza di tali sistemi, assicurando una conversione efficiente della potenza prelevata dalla rete, senza sprechi di energia. Ciò consente di progettare caricatori di bordo sempre più compatti, leggeri e affidabili.