Non ci sono prodotti a carrello.
di Bryan Padilla, Product Marketing Engineer, Texas Instruments
La progettazione di sistemi automobilistici può comportare un’enorme pressione a ridefinire i sistemi powertrain dei veicoli al fine di raggiungere gli obiettivi di riduzione delle emissioni di gas serra (GHG) stabiliti dalle iniziative dell’Unione Europea, degli Stati Uniti, Cina e Giappone, solo per citarne alcune. Per raggiungere questi obiettivi, alcune case automobilistiche stanno implementando sistemi a 48 V per veicoli mild-hybrid, ma la maggior parte sta passando dai tradizionali modelli con motore a combustione interna (ICE) ad un sistema di propulsione completamente elettrico, come mostrato nella Figura 1.
A causa degli obiettivi ambientali per la riduzione delle emissioni, si prevede che i veicoli elettrici (EV) aumenteranno rapidamente la loro quota di mercato nel prossimo decennio. Per velocizzare l’adozione dei veicoli elettrici, i fornitori di gruppi powertrain stanno progettando powertrain elettrici integrati e completi di inverter di trazione, convertitore CC/CC e caricabatterie di bordo in un unico pacchetto. Sebbene questo approccio riduca il peso del veicolo, abbassi i costi complessivi e fornisca una maggiore densità di potenza, richiede anche una maggiore attenzione alla gestione termica, in quanto densità di potenza più elevate e fattori di forma più piccoli aumentano la temperatura di esercizio, il che può degradare le prestazioni del sistema powertrain o, peggio ancora, danneggiarlo. I sensori di temperatura sono sempre stati un componente necessario all’interno dei powertrain dei veicoli, ma poiché spesso vengono ripensati o riutilizzati nei progetti per anni, il loro impatto positivo sui sistemi powertrain elettrici è stato limitato. La nuova tecnologia dei sensori di temperatura, con una corretta implementazione, può avere un forte impatto sull’efficienza e sull’affidabilità dei sistemi powertrain elettrici integrati.
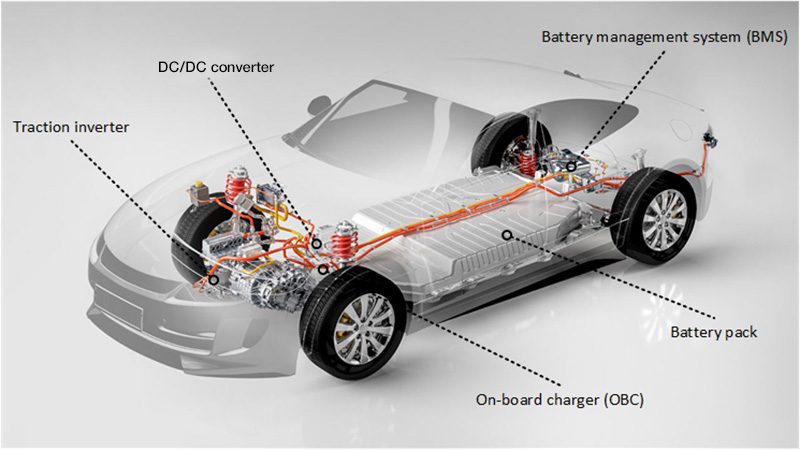
Figura 1: Sistemi powertrain elettrici
Maggiore precisione della temperatura per contribuire ad aumentare l’efficienza dei powertrain elettrici integrati
I consumatori vogliono che i veicoli elettrici si ricarichino più rapidamente e abbiano maggiore autonomia con una singola ricarica. A tal fine, i progettisti devono aumentare l’efficienza del gruppo powertrain elettrico integrato. Uno degli approcci possibili consiste nell’aumentare i livelli di tensione e le frequenze di commutazione all’interno degli stadi di potenza. Tuttavia, farlo con un ingombro così ridotto intensifica la densità di potenza e provoca un aumento delle temperature, aumentando il rischio di fuga termica. Ottenere questo aumento di efficienza limitando il rischio di danni termici richiede l’uso corretto di sensori di temperatura accurati e circuiti di feedback di raffreddamento attivo.
[boris]
Spingere in modo sicuro i componenti fino alle loro massime prestazioni si traduce generalmente in temperature di esercizio più elevate e più vicine ai limiti del dispositivo. Come mostrato nella Figura 2, massimizzare la precisione del sensore consente al processore di ridurre al minimo il margine di errore di sicurezza della temperatura, in modo da poter controllare con maggiore precisione alcune funzioni come la ricarica del veicolo e il flusso di potenza, anche quando ci si avvicina ai limiti termici d’esercizio dei dispositivi.
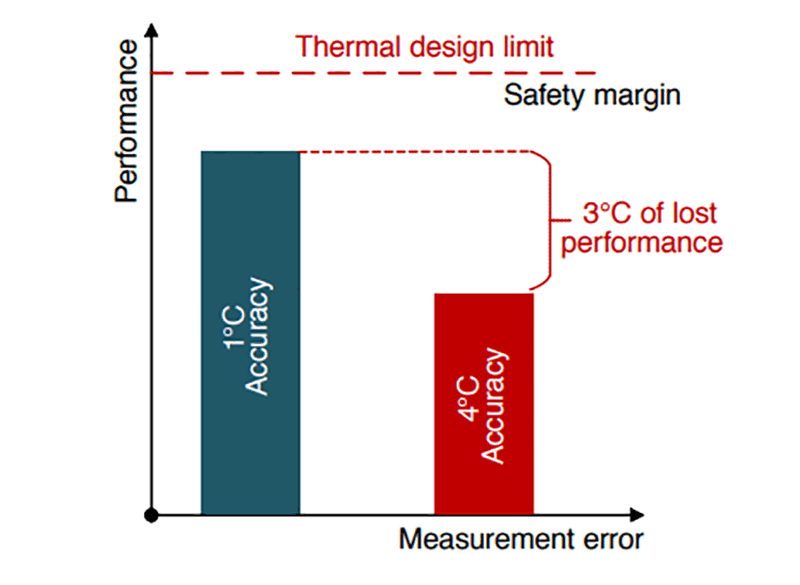
Figura 2: L’effetto della precisione sui margini di sicurezza
Il contributo dei sensori di temperatura a bassa deriva nel mantenere nel tempo l’affidabilità dei sistemi powertrain integrati
I consumatori vogliono che i loro veicoli durino nel tempo. La durata dell’elettronica contenuta in un powertrain elettrico integrato è direttamente correlata alle temperature a cui è esposta. Per mantenere per molti anni il corretto funzionamento di componenti come i transistor ad effetto di campo dello stadio di potenza, i sensori di temperatura devono essere affidabili e presentare una deriva minima.
Molti componenti elettronici presentano una deriva con il passare del tempo e i sensori di temperatura non fanno eccezione. La deriva dipende molto dalla composizione del materiale di un sensore. Ad esempio, i sensori di temperatura a base di silicio presentano una deriva del sensore trascurabile nel tempo, mentre i rilevatori di temperatura a resistenza hanno una deriva che può avere qualsiasi valore tra ±0,1 e ±0,5°C all’anno; i tradizionali termistori a coefficiente di temperatura negativo (NTC), invece, hanno generalmente una deriva >5% con il passare del tempo (escludendo la deriva dei componenti esterni). A mano a mano che un sistema invecchia, la deriva dei sensori può aumentare l’errore della soluzione di rilevamento della temperatura e limitarne l’efficienza, obbligandone lo spegnimento prematuro o causando danni termici ai componenti.
Nel progettare prestazioni a lungo termine, per il sensore di temperatura è opportuno utilizzare un circuito integrato (IC) che fornisca un’accuratezza garantita sull’intero intervallo di temperatura d’esercizio, al contrario della discutibile accuratezza offerta da implementazioni discrete, come i termistori NTC, quando non sono calibrate. Un sensore di temperatura digitale come il TMP126-Q1 consente un monitoraggio preciso fino a valori estremi di 175°C con una precisione di ±1°C e fino a ±0,3°C su un ampio intervallo di temperature. Nel caso di transitori di tensione e picchi all’interno del sistema, le temperature possono aumentare piuttosto rapidamente.
Come illustrato nella Figura 3, il TMP126-Q1 aiuta il sistema a intraprendere un’azione preventiva attraverso il rilevamento dei picchi di temperatura, che possono essere un importante indicatore di problemi termici prima che la temperatura raggiunga livelli pericolosi.
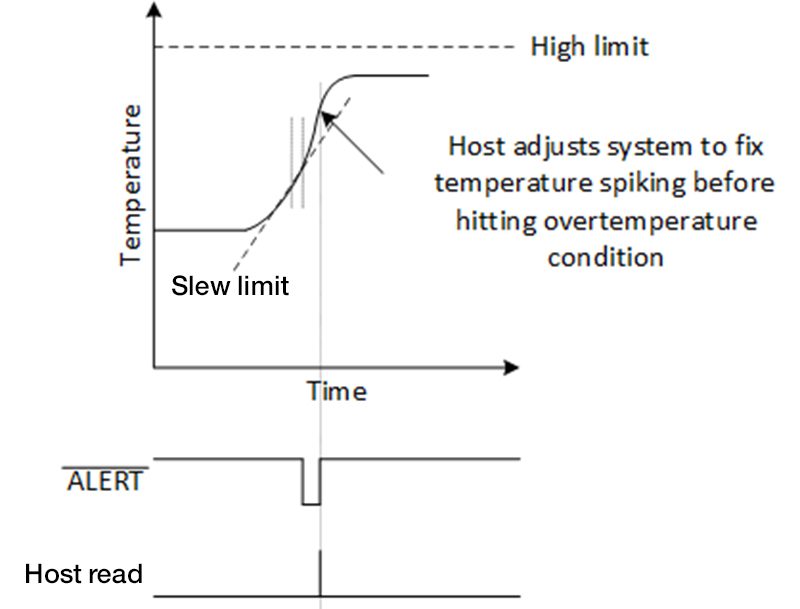
Figura 3: La nuova funzione di avviso dello slew rate nel TMP126
Come accennato in precedenza, si potrebbe cercare di aumentare le frequenze di commutazione per incrementare l’efficienza, ma questa operazione potrebbe portare a interferenze elettromagnetiche indesiderate (EMI). Per operare in condizioni con EMI elevate, il TMP126-Q1 dispone di un controllo di ridondanza ciclica integrato per garantire l’utilizzo dei dati solo in assenza di errori. Inoltre, il TMP126-Q1 viene fornito con la documentazione relativa al tasso FIT (failure-in-time) ed FMD (failure mode distribution) per la sicurezza funzionale, in modo da favorire il conseguimento della certificazione a livello di sistema. L’elevata precisione del dispositivo e la deriva trascurabile consentono ai gruppi powertrain integrati di ridurre i propri margini di protezione, portando a spegnimenti meno frequenti e proteggendo comunque il sistema dal surriscaldamento: il tutto, per ottenere una maggiore efficienza.
Conclusione
Non è una sorpresa il fatto di poter trovare oltre 20 sensori di temperatura distribuiti nei sistemi powertrain elettrici integrati. Un rilevamento accurato può aiutare a massimizzare l’efficienza di un sistema, prevenire false attivazioni dei sistemi di controllo e proteggere i circuiti integrati o altri componenti in modo più efficace. La capacità di conservare tale efficienza nel tempo e di consentire una maggiore vita utile su strada delle automobili è resa possibile dai sensori a deriva ridotta realizzati in silicio. Indipendentemente dal sensore di temperatura scelto, è opportuno sceglierne uno accurato e affidabile, seguire le best practice di posizionamento del sensore e sfruttare le nuove funzionalità dei sensore.
[/boris]